“Blended-wing” aircraft design promises 50% cut in fuel
Picture an airplane. Odds are you imagined something close to a Boeing 737, the most-produced aircraft in commercial aviation. Aircraft like this are built according to a basic blueprint: a tube-and-wing configuration, in which wings are attached to a cylindrical structure (the fuselage), which houses all passengers and cargo.
The aerospace industry has continually refined this design for nearly a century by improving the efficiency of engines, utilizing innovative materials, and optimizing aerodynamic shapes to improve performance and fuel economy.
But such improvements have a ceiling in terms of fuel efficiency — piercing it could require rethinking the basic shape of aircraft.
That’s the bet made by the U.S. Department of Defense, which recently awarded a $235 million contract to aerospace startup JetZero and partner Northrop Grumman, the developer of the B-2 stealth bomber, to develop a working prototype of a blended-wing-body (BWB) aircraft. The aircraft, called the Z-5, is expected to make its first flight in 2027.
If tests prove successful, the Air Force might use the design to develop more efficient refueling tankers and transport aircraft. The Z-5 — which the company says will have a range of at least 5,000 nautical miles and will carry up to 250 passengers — could also be used by commercial airlines beginning in the 2030s. (Commercial versions would have to come with folding wings, so that the Z-5 — which has a wingspan of nearly 200 feet, more than 80 feet wider than a 737 — could maneuver safely around airports.)
JetZero says its design will cut fuel burn and carbon emissions in half compared to conventional aircraft. The Z-5 aims to hit those numbers with reduced drag, engine size, and aircraft weight. But it will also offer the option to use engines that burn liquid hydrogen, which does not release carbon dioxide when burned, instead of standard jet fuel.
It remains to be seen whether JetZero will achieve those efficiency goals. But there’s reason to think BWB aircraft could help lower emissions in the aviation industry, which accounts for about 2% of global CO2 emissions.
A hybrid design: It’s no wonder the aviation industry has stuck with the tube-and-wing design for nearly a century: The configuration is aerodynamically efficient for cruising, provides a clear structure for passenger and cargo layout, and is well-understood in terms of stability and control dynamics.
But other shapes can offer specific advantages. A “flying-wing” design, for example, has no definite fuselage, opting instead for a boomerang shape that gives the craft extremely low drag and the ability to evade radar detection, like the B-2 stealth bomber.
A BWB aircraft falls somewhere between the flying-wing and tube-and-wing design. The BWB configuration blends the wings and fuselage into one continuous structure that reduces drag by minimizing the wetted area, which is the surface area of the craft that interacts with the outside airflow. NASA describes the benefits of the BWB design like this:
“The BWB airframe merges efficient high-lift wings with a wide airfoil-shaped body, allowing the entire aircraft to generate lift and minimize drag. This shape helps to increase fuel economy and creates larger payload (cargo or passenger) areas in the center body portion of the aircraft.”
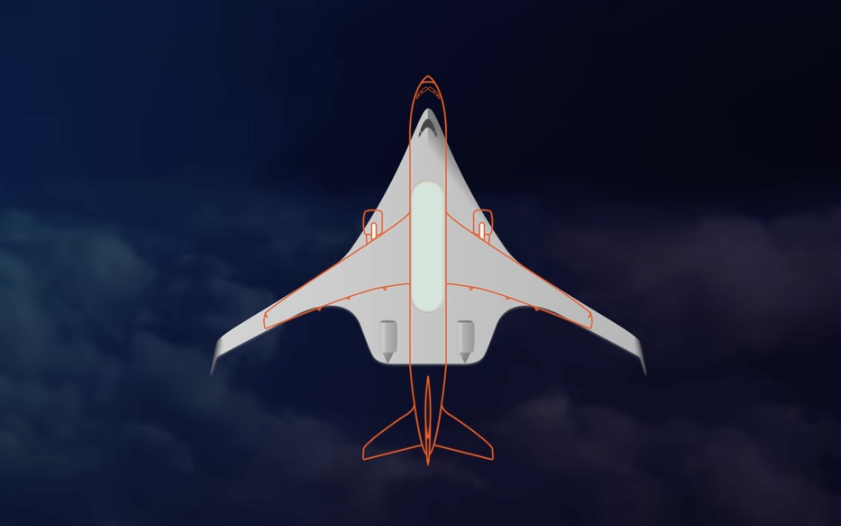
JetZero says this increased space — in the form of a wider cross-section — is key to housing the Z-5’s (optional) liquid hydrogen fuel tanks, which are too big to store inside tube-and-wing aircraft. Liquid hydrogen has a lower energy density than standard jet fuels, so more storage space is needed to deliver the equivalent amount of energy. For passengers, the wider cross-section would mean a much wider cabin — one with fewer but longer rows than in conventional airliners.
An opportunity for BWB aircraft: It’s worth noting that BWB aircraft aren’t an entirely new concept. The first designs for aircraft resembling the BWB design date back nearly a century. In recent decades, private companies and government agencies have developed a handful of BWB aircraft, including NASA’s remote-controlled X-48 (decommissioned in 2013) and Airbus’ experimental MAVERIC (unveiled in 2020). Still, BWB aircraft have yet to see widespread adoption.
One reason centers on difficulties with pressurization. It is relatively straightforward to pressurize a cylindrical fuselage, ensuring passengers and crew can breathe and stay comfortable at high altitudes. The irregular shape of the interior of a BWB aircraft makes it more difficult to distribute and maintain equal pressure throughout the cabin, considering that stresses from pressurization might be distributed differently across the aircraft.
JetZero says that new composite materials that are both light and strong have eliminated this obstacle for BWB aircraft. In an op-ed for Aviation Week, Kevin Michaels noted that JetZero also has the advantage of timing.
“The Z5 offers the potential of a rare ‘troika’ of enhanced national security, sustainability and economic benefit — all priorities in Washington,” Michaels wrote. “With interest from both civil and military customers, the Z5 could follow the path of the Boeing KC-135 and 707, where the Pentagon funded much of the aircraft’s development costs before commercializing.”
JetZero aims to enter the Z-5 into service in 2030.